When working on projects, Document Control is one of the roles that help control the project and help monitor its progress.
It is therefore an essential function to the Project Management team, providing them with the key performance indicators of the documentation.
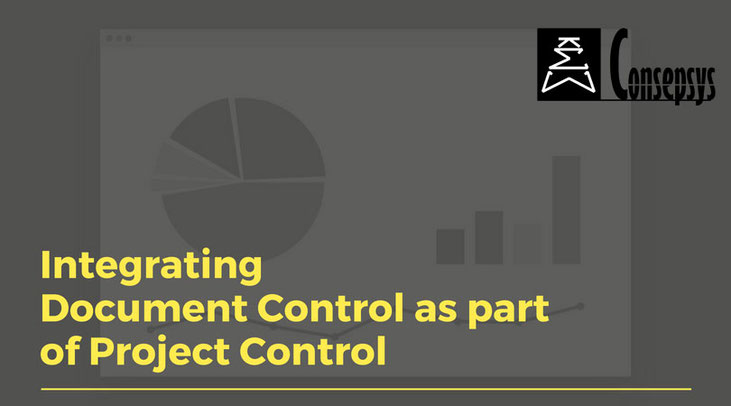
What are Project Controls?
Project Controls can be defined as the group of disciplines that plan, measure and monitor the project.
It is about monitoring the difference or gap between the planned variables and the actual performance.
An example, from the Cost Control area: We were planning expenditures of 125,000$ this month, but we actually spent 250,000$: what happened there? Does that come from an overspend or is it just expenditures planned for another month that came in early (or late)? Is there any corrective actions to take?
How does Document Control fit into Project Controls?
Document Control, when properly implemented and executed, is one of the key roles to help measure the performance of a project and its progress.
Indeed, the progress of most major projects is monitored through the provision of the agreed documentation deliverables.
To take a simplified example, if we were supposed to deliver 10 documents during the design phase of a project and we have delivered 5, then the progress is 50%.
And if we were supposed to send those 10 documents by a certain date, and this delivery is overdue, this is something the Project Manager needs to know as soon as possible.
How Document Control can help control the project?
- By issuing regular reports to the Project Management & Project Controls team, showing the progress of the documentation
- By keeping an up-to-date and accurate Document Control dashboard that displays the status of the documentation key performance indicators.
- By issuing, at least on a weekly basis, a report on late documents / late comments to the project team, so that they can take immediate action
- By keeping lines of communication open between Client Document Control team and Contractor(s)/Supplier(s) Document Control teams so that we can identify and fix easily any potential issue that may arise regarding documentation
- By issuing, at least on a weekly basis, the latest updated MDR (Master Deliverable Register) to the Client and asking them to cross check information. This helps identify gaps and potential issues
- By sitting down as early as possible with the Planner, in order to integrate the provisional dates for documentation delivery in our DC system. This helps then to measure where we are compared to where we were supposed to be.
- By ensuring that the Project Manager understands the Document Control team’s capabilities and how we can support him/her along the way.
- By discussing with project team their reporting needs as well as defining thresholds for red-flagging during the project
- By ensuring that project users receive an induction to the Document Control essentials at the start of the project, and that they know who to ask questions if they have any
- Finally, by ensuring that the mechanism for spotting and correcting non-conformities is in place.
Share this!
Share this!